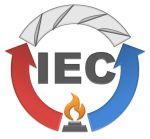
Scientific and research offer of the Department of Aeronautical Engineering
COMPUTATIONAL ANALYSIS
For numerical analyses, we use open source CFD software: OpenFOAM and SU2. It is possible to use commercial software (Ansys Fluent, Numeca), but this involves licensing costs.
Dedicated computational models are created in programming environments such as Python and C++ to support analytical design methods and to analyze momentum and mass heat transfer processes in problematic flow issues. Issues of this type are used in the design and analysis of: pumps, compressors, fans, injectors, injectors, nozzles, diffusers, wings, propellers, rotors and wind turbines.
The use of numerical fluid mechanics methods for:
- analyzing flows of low and high Mach numbers; analyzing flows with heat and mass exchange;
- analyzing flows with the generation of heat and mass from solid and liquid fuels;
- determining the size of mass flows; determining pressure losses in internal flows;
- analyzing external flows (determining aerodynamic forces, diagnostics flow field) convective heat exchange (gas/liquid cooling problems, heat exchangers, etc.) flow analysis of rotating machines (pumps, compressors, blowers, fans, turbines)
- analysis of the flow of non-Newtonian liquids in machine elements (oils, greases, cooling fluids)
DESIGN SERVICES
- Design of aerodynamic elements of machines and devices, e.g. design of devices that reduce the aerodynamic drag of road vehicles.
- Aerodynamic design of unmanned aerial vehicles in fixed-wing configuration; Design of propellers, rotors and rotors of HAWT wind turbines. Design of valves, chokes, injectors and other elements of installations transferring liquids or gases in terms of both incompressible and compressible flows.
- Modernization projects through geometric modifications of ready-made machines, devices, rooms in terms of aerodynamic optimization.
- Design of flow elements of pumps, fans, blowers, compressors and turbines; Geometry optimization (shape modifications to obtain a minimum of resistance, pressure losses or obtaining the desired pressure distribution).
- Designing the geometry of nozzles, swirlers, diffusers, injectors for flows in the compressible range.Selection of the geometry of flow devices for multiphase flows (cavitating nozzles, injectors, etc.) based on the HEM model (homogenous equilibrium model).
- Calculation pressure losses and determining loss coefficients in pipeline systems, selection of flow devices for given flow systems. Advanced numerical modeling of turbulence (LES, DES, DDES analyzes) (Fig. 1).
Fig. 1. Streamlines at the top of the transonic compressor solved using the DDES method
EXAMPLES OF RESEARCH IMPLEMENTATIONS
- Performing the process of numerical optimization of the UAV propeller in order to reduce acoustic emissions while maintaining the original performance.
- Development of the structure of curtains in the space of the convection chamber based on simulation tests (Fig. 2).
Fig. 2. Velocity distribution in the drying chamber on control surfaces
- Development of a lightweight truck trailer design with reduced aerodynamic resistance
Fig. 3. Speed distribution of a truck trailer
- Development of an open-type swirl injector design for a hybrid sounding rocket
Fig. 4. Liquid distribution in the oxidizer injector of a hybrid rocket engine.